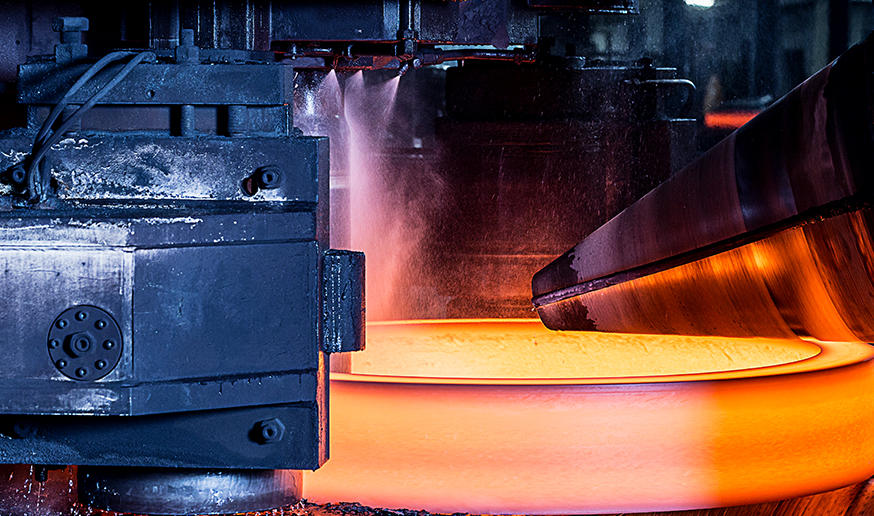
Nella forgiatura dei cilindri idraulici vengono comunemente utilizzati diversi materiali, ciascuno dei quali offre proprietà uniche che possono influire sulle prestazioni:
Spesso utilizzato per la sua resistenza e convenienza, l'acciaio al carbonio è adatto per un'ampia gamma di applicazioni. Fornisce una buona resistenza all'usura e durata, rendendolo ideale per un uso intensivo. L'acciaio legato offre proprietà migliorate come maggiore resistenza alla trazione, tenacità e resistenza alla corrosione e all'usura. Ciò lo rende adatto ad ambienti esigenti in cui sono richieste prestazioni elevate. Noto per la sua resistenza alla corrosione, l'acciaio inossidabile viene utilizzato in applicazioni in cui è comune l'esposizione ad ambienti difficili o sostanze corrosive. Offre durabilità e longevità, anche se a un costo maggiore rispetto all'acciaio al carbonio. L'acciaio al cromo fornisce un eccellente rapporto resistenza/peso e resistenza alla fatica, rendendolo adatto per applicazioni in cui la riduzione del peso e la durata sono fondamentali, come nel settore aerospaziale o delle corse. Anche se meno comune dell'acciaio, l'alluminio viene utilizzato in alcune applicazioni di cilindri idraulici in cui la riduzione del peso è una priorità. Offre una buona resistenza alla corrosione e conduttività termica, ma potrebbe non essere resistente come l'acciaio.
La selezione del materiale influisce sulle prestazioni del cilindro idraulico in diversi modi:
Resistenza e durata: i cilindri idraulici sono soggetti a notevoli sollecitazioni meccaniche, comprese pressioni elevate e carichi pesanti durante il funzionamento. La resistenza del materiale influenza direttamente la capacità del cilindro di resistere a queste forze senza deformazioni o cedimenti. Ad esempio, l’acciaio al carbonio offre robuste proprietà meccaniche, che lo rendono adatto per applicazioni che richiedono elevata resistenza alla trazione e resistenza ai carichi d’urto. Gli acciai legati, d'altro canto, forniscono proprietà meccaniche migliorate come maggiore durezza e tenacità, che sono vantaggiose in ambienti difficili dove la durabilità è fondamentale.
Resistenza alla corrosione: i cilindri idraulici spesso funzionano in ambienti diversi dove sono esposti a umidità, prodotti chimici e altre sostanze corrosive. I materiali con eccellente resistenza alla corrosione, come l'acciaio inossidabile o le leghe resistenti alla corrosione, vengono scelti per mitigare il rischio di degrado e guasti prematuri dovuti alla corrosione. L'acciaio inossidabile, ad esempio, contiene cromo, che forma uno strato protettivo di ossido sulla superficie, prevenendo ruggine e corrosione. Allo stesso modo, le leghe resistenti alla corrosione come gli acciai inossidabili Duplex o Super Duplex offrono una resistenza superiore alla vaiolatura, alla corrosione interstiziale e alla tensocorrosione indotta da cloruri, rendendoli ideali per applicazioni marine o offshore.
Resistenza all'usura: nelle applicazioni in cui i cilindri idraulici sono esposti a materiali abrasivi o forze di attrito ripetitive, la resistenza all'usura diventa una considerazione critica. Per ridurre al minimo i danni superficiali e prolungare la durata dei componenti, vengono utilizzati materiali con buone proprietà di resistenza all'usura, come leghe di acciaio temprato o trattamenti superficiali come la cromatura dura. Le leghe di acciaio temprato, compresi gli acciai al cromo-molibdeno (cromo), vengono trattati termicamente per ottenere un'elevata durezza superficiale, migliorandone la resistenza all'abrasione e all'usura. I trattamenti superficiali come la cromatura dura creano uno strato superficiale durevole e resistente all'usura che protegge il materiale sottostante dall'usura abrasiva.
Peso: in alcune applicazioni in cui la riduzione del peso è fondamentale, come nel settore aerospaziale, automobilistico o delle apparecchiature mobili, la densità del materiale influenza direttamente il peso complessivo dei gruppi di cilindri idraulici. I materiali leggeri come l'alluminio o il titanio offrono un notevole risparmio di peso rispetto alle leghe di acciaio convenzionali, senza compromettere le prestazioni meccaniche. Le leghe di alluminio, rinomate per la loro bassa densità e l'elevato rapporto resistenza/peso, sono comunemente utilizzate nelle applicazioni aerospaziali e automobilistiche per ridurre il peso del veicolo e migliorare l'efficienza del carburante. Allo stesso modo, le leghe di titanio offrono eccezionale robustezza e resistenza alla corrosione a una frazione del peso dell'acciaio, rendendole adatte per applicazioni sensibili al peso in cui prestazioni e durata sono fondamentali.